Elliptical-blade NACA airfoil propeller
![[Spitfire]](https://upload.wikimedia.org/wikipedia/commons/thumb/4/4d/Spitfire_CGYQQ_Y2K_SN_TE294.jpg/320px-Spitfire_CGYQQ_Y2K_SN_TE294.jpg)
Of all the kinds of drag that a wing or propeller blade experiences, induced drag is an unavoidable price for lift. Induced drag has nothing to do with the drag created by surface area, surface roughness, or thickness of the airfoil. Induced drag depends on the planform shape of the wing. It is also inversely proportional to aspect ratio (the ratio of wing length to airfoil average chord length). The optimal and most efficient wing planform shape to distribute lift and minimize induced drag, theoretically, is an ellipse. Another advantage to an ellipse is that the wing tip is quite small, which reduces drag from induced wingtip vortices.
It is possible to create an elliptical lift distribution over the length of a wing without actually having an elliptical planform, by adjusting the airfoil shape and angle of attack. Because the advantages to elliptical wings are often negated by other design considerations (such as wingtip washout to improve stall characteristics), it is more economical to fabricate tapered wings with straight edges, so this is how wings are designed nowadays. (In the case of the Spitfire, the decision to give it an elliptical wing had less to do with induced drag and more to do with being roomier near the wing root than a straight tapered wing, allowing the aircraft guns to be completely internal.)
While elliptical-wing aircraft are a thing of the past, modern propeller blades are still made with elliptical planforms, or approximately elliptical planforms, and sometimes the rounded end of the ellipse is truncated. For example:Elliptical planform blades (left) and truncated elliptical blades (right). Sources: PickPik and Wikimedia Commons
I want to make a pull-copter
As I wrote in my article about ergonomic handle design, my objective is to 3-D print an over-engineered pull-copter, a toy that drives a propeller when you pull a cord through a handle, to make the propeller fly into the air. I already over-engineered the handle to be an ergonomic design, and I over-engineered the pull cord gear teeth as well. For the propeller, instead of making a crude simple flat blades like other designs I have seen, I decided to go all-out and engineer a propeller that uses real-world propeller design features, such as an elliptical blade planform and using multiple NACA airfoil profile transitions along the length of the blades.
So let's start with the planform.
Propeller blade planform
Did you notice that the Spitfire wing in the picture above isn't a symmetrical ellipse? The trailing edge curves more than the leading edge. The same is true for propellers. This is because the thickest part of the airfoil cross-section is aligned in a straight line along the length of the wing or blade, for greater strength. In the case of a wing, one can manufacture a straight spar to fit along a straight line of maximum airfoil thickness. In the case of a propeller, this effictively provides a straight bar of material of maximum thickness running along the length of the blade. This thickness alignment requires distorting the ellipse, but the elliptical lift distribution remains unaffected.
A typical NACA airfoil is thickest at about 30%–40% of the airfoil chord from the leading edge (the "chord" is a line drawn between the leading and trailing edges of the airfoil). The interactive drawing below shows what the wing (or blade) planform looks like when an arbitrary "centerline" is defined as a percent of chord. A 50% centerline results in a symmetrical ellipse. A 30% centerline results in something that looks like a Spitfire wing.
Not the true planform
I refer to the propeller blade planform as the two-dimensional projection of the blade onto a planar surface. Imagine the propeller laying on the ground with the sun directly overhead. What I call the "planform" corresponds to the shadow cast by the propeller blade. A flat blade with no tilt casts an elliptical shadow. However, a real propeller blade is twisted, not flat. Why must the blade be twisted?
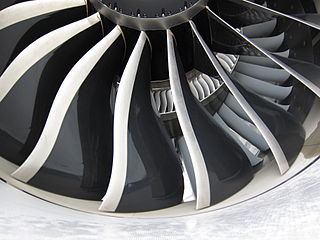
Turbine blades showing their twist for acheiving constant pitch. The angle of attack near the hub is much steeper than at the tips. Source: Oliver Cleynen, Wikimedia Commons.
Imagine the propeller screwing itself through a solid medium with no slippage. The amount of forward movement for a single complete rotation of the propeller is called the pitch of the propeller. A propeller blade is twisted so that the angle of attack of the airfoil at any point along the length of the blade results in the same forward movement of the propeller. Aircraft propellers typically have a pitch ranging from about 75% to 150% of the length of the propeller blade. Lower-pitched propellers are called "climb" props and higher-pitched propellers are called "cruise" props, because their pitch is optimized for rapid climbing or fast cruising, respectively. A "climb" prop doesn't cruise fast, and a "cruise" prop doesn't let the aircraft climb fast. More advanced aircraft have variable-pitch propellers to provide optimal performance in any situation.
If the propeller is laying flat on the ground, so that it would fly straight up if it spins, the angle of attack near the center of rotation is nearly vertical, and the angle of attack at the tip is shallower. For a desired pitch \(p\), the airfoil angle of attack \(\alpha\) at radial position \(r\) from the center of rotation is given by:
$$\alpha = \tan^{-1}\left(\frac{p}{2\pi r}\right)$$Notice that as \(r\) approaches zero in the denominator, the inverse tangent argument goes to infinity, resulting in the attack angle approaching π⁄2 (90°).
Obviously, twisting the blade toward 90° the closer it is to the hub results in a narrower shadow there.
Blade profile demo
In addition to setting the centerline at an optimum place, the blade planform can be adjusted further. The blade length doesn't have to be the ellipse length. It can be truncated. We can define the ellipse length as a multiple of the blade length, and we can control the blade width by controlling the eccentricity (ratio of width to length) of the ellipse. Adjusting the blade pitch (0=flat) shows how the blade profile deviates from an ellipse due to twisting. Finally, we can determine a sweep angle per unit length to offset the airfoil by a small angle in the blade's arc of travel.
This interactive demo lets you play with these parameters. The center of rotation of the propeller is the black circle on the left.
Blade pitch:
Ellipse width: % of blade length
Centerline: %
Ellipse length fraction:
Degree sweep per length unit: °
Using these control parameters, one can define blade planforms for just about anything: aircraft propellers, wide-bladed boat propellers, or computer cooling fans.
Constraints on airfoil chord
The elliptical planform shape gets distorted even more when accounting for the dimensional constraints. A planform with a low aspect ratio (a short wide propeller blade) may have a short hub, but the airfoil near the hub is at a high angle of attack and would extend beyond the ends of the hub. Therefore, the airfoil must be shorter to attach physically to the propeller hub.
Simply limiting the chord length so that it never exceeds the fore and aft boundaries of the hub results in a corner appearing in the blade outline at the radius where this constraint goes into effect. The picture below shows what happens when the angle of attack gets steep enough nearer to the hub to limit the length of the chord, which wants to be longer because an ellipse-shaped blade is widest at the hub.
A better approach is to constrain the airfoil chord to fit inside an ellipse having its two axes being the length of the hub and the width of the elliptical blade planform at any radial distance from the hub. A chord is drawn through the center of this ellipse at the angle of attack corresponding to the distance from the hub. The length of this chord becomes the chord length of the airfoil. Constrained this way, the blade becomes slightly narrower far from the hub where the hub length constraint wouldn't normally occur, but overall we get a nice smooth profile, as shown here:
NACA airfoils
There are an infinite variety of airfoils. The NACA airfoils were developed by the National Advisory Committee for Aeronautics (NACA) starting in the 1930s. There are effectively an infinite variety of NACA airfoils too. The NACA 4-digit airfoil series has been popular for nearly a century, although more sophisticated NACA designs have been developed: 5-, 6-, and 7-digit series, as well as an "8" series for supercritical airfoil applications. The 4-digit series is fairly simple and easy to understand, it has good lift and drag characteristics, and is still used in propeller designs for general aviation aircraft.
I read recently that the NACA 6412 is popular for propellers. Let's call those four digits CMTT. They represent three numbers, all of which describe a fraction of the chord length of the airfoil:
- The first digit (C) is the maximum camber as percentage of the chord. If C=6, the maximum camber is 6% of the chord.
- The second digit (M) is the distance of maximum camber from the airfoil leading edge, in tenths of the chord. So if M=4, the maximum camber occurs 40% of the distance from the leading edge to the trailing edge of the airfoil.
- The last two digits (TT) describe maximum thickness of the airfoil as percent of the chord. If TT=12, then the maximum thickness is 12% of the chord length.
A good explanation of the equations to calculate the curves of the airfoil are given in Wikipedia as well as AirfoilTools and many other places, so I won't reproduce them here. Just click on those links if you want to see them.
For 3-D printing purposes, I introduced a gradual expansion of the thickness from the airfoil's leading to its trailing edge, to provide a little bit of extra thickness at the trailing edge to accommodate the width of a perimeter laid down by the printer. The trailing edge thickness is then constant regardless of the size of the airfoil.
Transitions along the blade
A propeller blade doesn't have the same airfoil cross-section across its length. For structural reasons, it typically has a short, thick airfoil where the blade attaches to the hub, often with fillets for a smooth structural joint. This root airfoil then transitions to the blade's intended airfoil cross sections, which transition through varying degrees of thickness and camber toward the tip.
For my propeller blade design, I decided to base it on a NACA 6412 like many real-life propellers, but start with a thick NACA 8430 airfoil where the blade joins to the hub, transitioning to a NACA 6412 one-third of the way toward the tip, and then transitioning to a slightly different profile (NACA 4412) at the tip of the blade. The NACA 4412 has just a little bit less camber to maintain some thickness for 3-D printing at the blade tip.
The transitions aren't linear. I use a sine function from the hub to the first transition point, so the thick airfoil changes quickly at first and then the transition interpolation flattens out at the peak of the sine curve where it becomes the middle airfoil profile. From there it continues a sine function interpolation that starts out flat and has its steepest change near the tip. In this way, a large portion of the blade approximates the middle airfoil profile.
Initially I wasn't sure if the airfoil cross sections should be planar or warped around the hub. Eventually I elected to warp them. A thick airfoil can wrap around on itself at low radius values, so I included a minimum radius equal to the radius of the hub. I also came up with a way to make a smooth fairing between the root of the blade to the hub.
Here is a collection of examples I made in OpenSCAD using the same parameters as described above.
My OpenSCAD propeller library is available at Thingiverse and Printables.
You don't actually want an elliptical lift distribution or planform; you want to design for Minimum Induced Loss.
ReplyDeleteSee e.g.
https://core.ac.uk/download/pdf/42869761.pdf and its references, and
https://arc.aiaa.org/doi/10.2514/3.23779
There are some free tools which may be of interest to you e.g. https://www.mh-aerotools.de/airfoils/javaprop.htm
Hi, thanks for the comment, and for those references! Actually the aerotools.de site was one of the inspirations for embarking on this project that resulted in this article here. While the scholarly papers you reference do say that an elliptical lift distribution is desirable, you are correct that simply using a twisted ellipse planform for a propeller blade may not result in the minimum induced loss. This article was more of a thought experiment that deliberately did not go into complex mathematics, however, and the results in the last picture above do "look" reasonable for real-life propellers.
DeleteI think this is the best, clearest, most helpful and illuminating article I have ever read on these subjects. Thanks and congratulations.
ReplyDeleteI was looking for a low pitch prop to push a heavy displacement boat at a slow speed. You saved me days. Thanks
ReplyDeleteHey any suggestions for finding the moment of inertia/center of mass for a uniquely designed prop blade like the one you made?
ReplyDeleteIt would be possible, but rather involved, to calculate the geometric centroid of the complex polyhedron shape that makes the blade. However, the best option might be to export an STL file of one blade and then use another program like Blender to find the center of mass.
ReplyDeleteCenter of Mass can also be calculated - for any STL - with a function in Meshmixer (free software): Analysis > Stability.
DeleteCould you perhaps expand in detail about how you used the sine function to transition across the whole blade? Did you do any calculations with it?
ReplyDeleteThe sine function starts at z=0 (blade hub), rises to a maximum of 1 at z=π/2 (middle of the blade), and falls back to 0 at z=π. These sinewave values between 0 and 1 are used as interpolation proportions. For the inner half of the blade, given an interpolation proportion p between 0 and 1, and airfoil profiles (a list of coordinates) a0 at the root and a1 at the midpoint, the interpolated airfoil coordinates would be a=p(a1-a0)+a0. For the outer half of the blade with airfoil profile a2 at the tip, the interpolated airfoil coordinates would be a=p(a1-a2)+a2. By using sinewave values instead of linear values along the length, you get a smooth nonlinear transition instead of a sharp transition in the middle.
DeleteHow do i set the pitch ? For example an 17" x 6" propeller?
ReplyDeleteIn this article, and in the OpenSCAD software linked (at Printables and Thingiverse), the pitch is expressed as a percentage of blade length. A 17" diameter propeller has a radius (blade length) of 8.5". Therefore, 6" pitch would be 6/8.5, or 70.6%.
Delete